Mastering Inventory Valuation for Enhanced Financial Management
Gain insights into the complexities of inventory valuation methods and their effects on your financial statements.
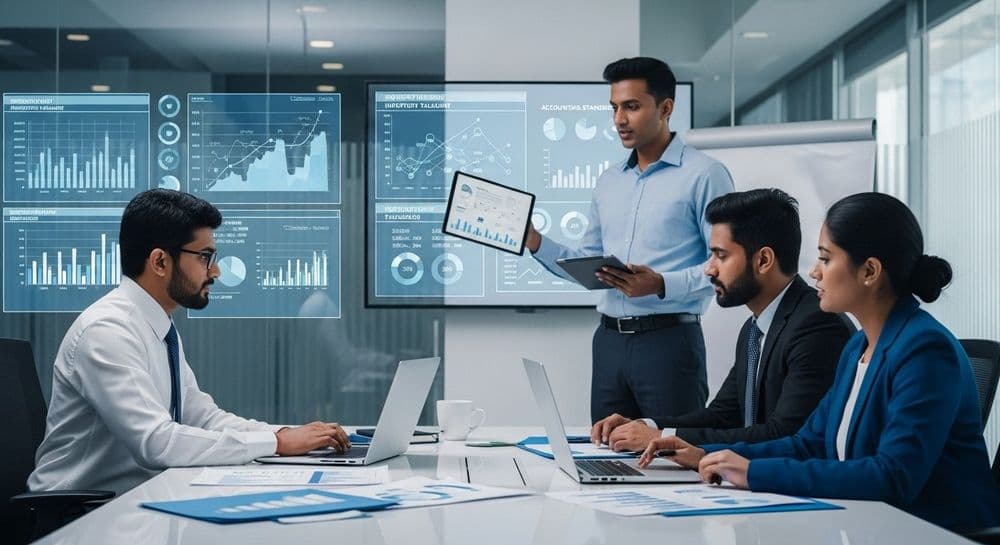
Companiesinn
Created: 11th July, 2025 10:02 AM, last update:11th July, 2025 10:02 AM
Article Content
Introduction to Inventory Valuation
Inventory valuation is a vital component of accounting that significantly influences the financial health of any organization. It involves the methods and standards used to assess the value of inventory on financial statements. This article aims to simplify the complexities surrounding inventory valuation, including its definition, methodologies, and the factors that affect its assessment.
What Constitutes Inventory?
Definition of Inventory includes:
- Finished Goods: Items that are ready for sale in the regular course of business.
- Work in Progress: Products that are partially completed and not yet available for sale.
- Raw Materials: Basic components utilized in the production process that will be consumed during the manufacturing of goods.
Understanding Net Realizable Value (NRV)
Net Realizable Value (NRV) is a key concept in inventory valuation. It represents the estimated selling price of inventory in the normal course of business, minus any costs necessary to complete the sale. Grasping NRV is essential for businesses to effectively determine how to value their inventories.
Methods of Inventory Valuation
Inventory valuation is typically carried out using the lower of cost or net realizable value. Here are the essential steps involved:
- Calculate the Cost of Inventories: Identify all costs related to acquiring or producing the inventory.
- Evaluate the Net Realizable Value: Estimate the selling price and subtract any costs associated with completion and sale.
- Compare Values: Choose the lower value between the cost and NRV to establish the inventory's value.
Components of Inventory Cost
1. Purchase Cost
The purchase cost of inventory encompasses:
- The actual amount paid for the inventory.
- Non-recoverable taxes and duties.
- Freight charges incurred to transport the inventory to its current location.
- Any other expenses directly linked to the acquisition of the inventory.
2. Cost of Conversion
Cost of conversion refers to all expenses incurred to transform raw materials into finished goods. It includes:
- Direct Costs: Costs directly associated with production, such as labor.
- Fixed Overhead Costs: Indirect costs that remain constant regardless of production levels, like equipment depreciation.
- Variable Overhead Costs: Costs that fluctuate with production levels, such as packaging materials.
3. Other Associated Costs
Additional costs may include design expenses for custom orders and allocations for by-products generated during manufacturing. However, certain costs should be excluded, such as:
- Abnormal waste materials.
- Selling and distribution expenses not essential for production.
- Normal losses incurred during production.
Conclusion
Accurate inventory valuation is crucial for precise financial reporting and effective inventory management. By comprehending the definition, components, and methodologies of inventory valuation, businesses can make informed decisions that enhance their financial standing and operational efficiency. For further insights on business management, explore our guide on MSME Registration Process in India and learn how to register a Private Limited Company in India. Additionally, understanding trademark registration can safeguard your business's intellectual property as you expand.
Frequently Asked Questions
What are the different types of inventory in accounting?
In accounting, inventory mainly consists of three types: finished goods, work in progress, and raw materials. Finished goods are items ready for sale, directly available to customers. Work in progress includes products that are partially completed and not yet ready for sale. Raw materials are the basic components used in manufacturing, which will eventually be transformed into finished goods. Understanding these categories is essential for accurate inventory valuation and financial reporting.
What is Net Realizable Value (NRV) and why is it important?
Net Realizable Value (NRV) is an essential concept in inventory valuation that represents the estimated selling price of an inventory item minus any costs required to sell it. It's crucial for businesses to determine the value of their inventories accurately. By understanding NRV, companies can avoid overvaluing their inventory on financial statements, which can lead to misrepresentations of their financial health. It helps in making more informed decisions about pricing, production, and inventory management.
What are the steps to evaluate inventory using the lower of cost or NRV method?
To evaluate inventory using the lower of cost or net realizable value (NRV) method, follow these steps: First, calculate the total cost of the inventory, which includes purchase costs, taxes, freight charges, and any other directly related expenses. Next, determine the NRV by estimating the expected selling price and subtracting any costs associated with completing the sale. Finally, compare the calculated cost and NRV values, and record the lower amount as the inventory value. This method ensures you present a more accurate and conservative view of your inventory on financial statements.
What constitutes the purchase cost of inventory?
The purchase cost of inventory includes several components. Primarily, it encompasses the actual price paid for the inventory itself. Additionally, it involves non-recoverable taxes and duties associated with the purchase, as well as freight charges incurred to transport the inventory to its location. Any other expenses directly linked to acquiring the inventory also form part of the purchase cost. Being aware of these components ensures accurate inventory valuation and helps maintain precise financial reporting.
How do conversion costs affect inventory valuation?
Conversion costs play a significant role in inventory valuation as they represent all expenses incurred to transform raw materials into finished goods. These costs include direct costs, such as labor directly tied to production, and overhead costs, which can be fixed (like equipment depreciation) or variable (like packaging materials that change with production levels). Understanding and accurately calculating conversion costs is vital, as they contribute to the overall valuation of finished goods inventory, impacting financial statements and business decisions.
What costs should be excluded from inventory valuation?
When valuing inventory, it's important to exclude certain costs to ensure accurate financial reporting. Costs that should not be included are abnormal waste materials generated during production, selling and distribution expenses that are not essential for the manufacturing process, and normal losses that occur during production. By excluding these costs, businesses can present a clearer picture of their inventory value, which supports better financial management and decision-making.
Why is accurate inventory valuation crucial for businesses?
Accurate inventory valuation is vital for several reasons. It directly impacts financial reporting, affecting key metrics like profit margins and cash flow. Precise valuation helps businesses avoid overstatement of assets, ensuring compliance with accounting standards and maintaining investor confidence. Additionally, understanding inventory value aids in effective inventory management, allowing businesses to make informed decisions regarding purchasing, production, and sales strategies. Ultimately, accurate inventory valuation contributes to a business's overall financial health.
Start Your Business Today
Complete company registration with expert guidance